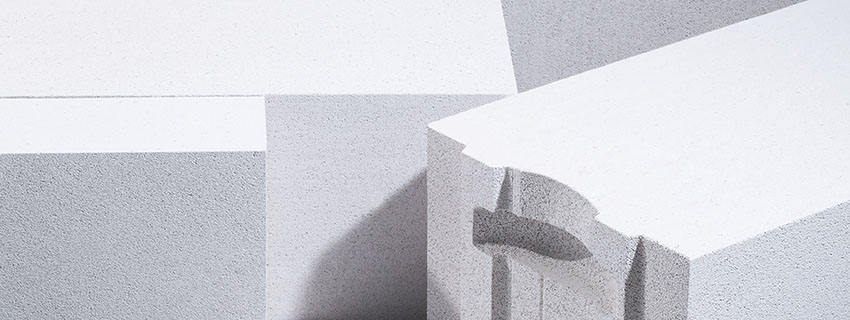
ТЕКУЩАЯ СИТУАЦИЯ
Газобетон весьма привлекательный материал на мировом рынке. Его производство в мире растет на 5 млн. м3 ежегодно, в то время как, согласно H. Bagheri (2006), общий спрос в 2010 г. достигнет 100 млн. м3. Это высококлассный строительный материал, созданный на основе простого сырья или даже отходов (песок и/или зола-унос), с незначительным количеством вяжущих материалов (известь, цемент). Порообразование, обычно, осуществляется при помощи алюминиевого газообразователя. Вспучивание материала активизируется посредством хорошо адаптированного производственного процесса при нормальных условиях, – это пример современного тренда в экономии. Последующее автоклавирование изделий под давлением (при около 10 МПа и 180-200°C, на протяжении около 10 часов) превращает химические минералы в прочную кристаллическую структуру – тоберморит. При этом удельное потребление энергоресурсов относительно низкое. Резка струнами очень аккуратная, что придает изделиям точную геометрию для укладки на клеевую смесь (толщина шва 1-3 мм). В строительной практике, чаще всего, применяется газобетон с плотностью в сухом состоянии от 275-400 кг/м3 (теплоизоляционное назначение) до 400-750 кг/м3 (конструкционно-теплоизоляционное назначение). Газобетон используется для кладки несущих стен или в целях утепления, а также для конструктивных элементов, таких как перемычки, стеновые панели и плиты перекрытия и покрытия. При уменьшении плотности материала величина усадки увеличивается. Это имеет очень важное влияние на несущие стены с низким уровнем армирования. На практике, плотность 400-500 кг/м3 является идеальным компромиссом в таких случаях.
Горизонтальные элементы (плиты перекрытия и покрытия) имеют армирование в зоне сжатия, что обеспечивает необходимую долговечность. Исследование плит возрастом до 70 лет подтверждают этот факт. Низкая плотность может компенсироваться большим содержанием стали, что преследует 4 цели: сопротивление напряжению, сжатию, сдвигам и сцепление. Диапазон длины плит традиционно был в пределах 6 м. Количество стали тогда было довольно умеренное. Увеличение размеров неизбежно привело к увеличению использования стали. «Siporex», шведский производитель, расширил опалубку до 8,0 м, но на практике лимит был 7,2 м с плотностью 500 или 600 кг/м3 [Lättbetonghandboken, 1993]. Критичным фактором был прогиб под статической нагрузкой – тестируемый элемент с длиной в 8,0 м имел значительный прогиб.
ТЕХНОЛОГИЯ «BCE»
Кардинально новым решением проблемы максимальной длины плит было предложение проекта «Block Composed Element» («BCE») – это технология, изначально предложенная одним из авторов в начале 1990-х [Hellers B.G.& Lundvall O., 1992]. Это гибридное соединение газобетона (на золе-уноса или песке), и «High-Performance Concrete» «HPC» (высокомарочный бетон) и имеет особый интерес для производителей блоков, который хочет расширить свое производство до полной системы строительства. Общая идея «BCE» была расширить диапазон размеров плит из газобетона до 9,0 м для панелей перекрытия и 12,0 м для панелей покрытия. Изделия состоят из элементов, функционирующих совместно в вертикальном и горизонтальном направлениях на втором этапе производства. Совместимость достигается посредством предварительного напряжения, которое выполняется «HPC»-компонентом, в то время как газобетон является компонентом, определяющим размеры и форму готового изделия. Предварительное напряжение необходимо для уменьшения деформации под нагрузкой. Это производство хорошо адаптировано под условия системы проектирования CAD/CAM, применимые к конкретному проекту. Это позволяет уменьшить финансовые затраты, т.к. бетон хорошо работает на сжатие, а сталь необходима для работы на изгиб и устойчивость. Таким образом, три из четырех требований к использованию стали в газобетонной панели обеспечены. Обычно, со стороны газобетона 75% стали экономится [Aroni, 1993], в то время как 75% цемента и половина потребляемой энергии экономятся со стороны цемента (HD-элементы, пустотелая опалубка). Это указывает на то, что переходя от тяжелого бетона на «BCE», мы уменьшаем половину выбросов углекислого газа. Сложность появляется при использовании двух различных видов бетона. Проект «BCE» все еще развивается.
КРАТКОЕ ОПИСАНИЕ ХАРАКТЕРИСТИК
- Энергозатраты на производство газобетона относительно ниже: 1,0 ГДж/м3 (одна треть от цемента);
- Плотность газобетона варьируется между 275 кг/м3 (теплоизолирующие качества) и до 750 кг/м3 (конструкционные качества);
- Теплопроводность (Вт/м∙K) теплоизоляционного газобетона на практике 0,08 (D275), 0,09 (D350), 0,10 (D400);
- Прочность на сжатие (Н/мм2) газобетона: 2,3 (D450), 3,0 (D500), 5,0 (D600), 10,0 (D750) (на цементе);
- Прочность на сжатие (Н/мм2) газобетона: 2,9 (D460), 3,6 (D600), 7,3/8,7 (D750) (на золе-уноса);
- Усадка (мм/м): 0,5 (D750), 0,7 (D600), 1,0 (D500), 1,5 (D450) (на цементе);
- Армированные плиты производятся из газобетона до 6,0-7,2 м длиной (на цементе). Армированные панели не могут быть произведены на золе-уноса;
- Армированные панели производятся на основании гибридной технологии («HPC» бетон и газобетон: на золе-уноса или песке) до 9,0 м длиной (плиты покрытия кровли до 12,0 м);
- Модуль упругости (Н/мм2): 1200 (D450), 1700 (D500), 2500 (D600), 4000 (D750).
ИСТОРИЯ ГАЗОБЕТОНА
Все началось в 1923 году, когда шведский архитектор Аксель Эрикссон, можно сказать случайно, обнаружил возможность использовать процесс автоклавирования для стабилизирования смеси сланца и обожженного известняка, при вспучивании смеси с помощью алюминиевой пудры. Усадка была минимальная (в старых изданиях [Ytong, 1942] говорилось, что усадка нулевая!). В 1924 году изобретение получило патент, но только через 5 лет, в 1929 году, оно стало использоваться в коммерческих целях компанией «Yxhults stenhuggeri AB», которая занималась кладкой природного камня, а позже переквалифицировалась в производителя искусственных каменных блоков. Это был смелый шаг предпринимателя Карла Августа Карлена, который вскоре окупился сполна, т.к. рынок как раз активно нуждался в стеновом материале с теплоизоляционными свойствами. После 2-й мировой войны Швеция претерпевала огромную нехватку энергоносителей.
«Ytong», так назвали материал после 1940 г., широко использовался благодаря сочетанию желаемых свойств, несущей способности, тепло- и звукоизоляции, огнестойкости, прочности, водонепроницаемости и стойкости к вредителям. Армированные элементы начали производить после 1933-34 гг. Армированные перемычки, которые представляли собой обычный ж/б элемент на обычном цементе, который с обеих сторон накрывался газобетоном [Ytong, 1942]. По нашей информации, это первый случай гибридного сочетания двух видов бетона, идея, которая сейчас дублируется в «BCE» системах. Однако «Ytong» все же остался производителем блоков. Быстрый успех продукта Эрикссона вызвал огромную конкуренцию. В случае «Carlsro kalkbruk» в Skövde, эта конкуренция носила дружеский характер и была основана на обмене опытом. Один из конкурентов производил простые пенобетонные блоки с 1924 г. [Rönnow, 1948] и впоследствии, следуя примеру «Yxhult», инвестировал в автоклавы с целью стабилизировать продукт. Модернизированное производство автоклавного газобетона началось в 1932 г. Название компании сменилось на «Skövde Gasbetong AB» в 1943 г. и затем на «AB Durox» в 1964-65 гг., название было взято из названия продукта.
Название «Durox» сейчас относится к датской группе. Компания все еще производит газобетон на 10 заводах по всему миру, из которых 9 находятся в Европе. Более серьезная конкуренция разразилась, когда продукт под названием «Siporit» (с 1937 г. «Siporex») появился на шведском рынке в 1934 г. [Rosenborg, 1998]. Этот продукт производился по рецепту на цементном вяжущем, как альтернатива старому составу сланца/извести, которые использовал Эрикссон и другие. Изначально, целью компании «Siporex» было сформировать полную систему строительства, включающую в себя как простые блоки, так и армированные продукты. Перемычки появились для элементов крыши через год (1935). Обычно, количество армированных продуктов компании «Siporex» превышало 60% (1964), в то время как объемы производства армированных элементов «Ytong» были намного меньшими. В европейских масштабах, это соотношение оставалось низким, 16% в 1991 г. [Dubral, 1992], что указывает на тот факт, что армированный газобетон, как материал, был применим на довольно низком уровне. Считается, что в настоящее время тенденция использовать армированный материал, формируя компоненты строительных систем, демонстрирует технологию строительства на более высоком уровне. Также, современная архитектура при дизайне проекта предпочитает свободное использование строительных материалов любых нестандартных размеров.
Датская группа «H+H A/S» (Henriksen og Henriksen Aktieselskab) была основана в 1937 г. Позднее произошло ее слияние с британской компанией «Celcon Ltd.» и на сегодняшний день она активно расширяет свое влияние в Западной Европе посредством выкупа производственных площадей, где после Второй Мировой Войны получили развитие технологии газобетона с применением золы-уноса. Компания «Celcon» стала инициатором использования золы-уноса, заменив им кварцевый песок в своем производстве, начиная с 1955 г. Широкое распространение технологии производства автоклавного газобетона во всем мире указывает на то, что рынок созрел для такого продукта, а также на то, что установить патентное право на продукт довольно сложно. Это давно пытается сделать компания «Ytong AB», с которой конкурирует «Siporex AB». Они пришли к временному перемирию. Тем временем другие производители, такие как «H+H A/S», попытали свое счастье на рынке и одержали успех.
ИНИЦИАТИВА КОМПАНИИ HEBEL
Еще один рецепт производства газобетона, третий, который, как и «Siporex» [Rosenborg, 1998], появился, вероятнее всего, под влиянием немецкого материала «Mikroporit», был разработан в технических университетах в Аахене и Штутгарте после 1942 г. [Schramm, 2005]. Наиболее вероятно, что вдохновение пришло от патента «Siporex» в 1937 г. Вопрос о том, были ли нарушены права собственности, согласно военного времени, все еще остается открытым. Но исследователи, конечно же, понимали чувствительность традиционных деревянных полов к военным действиям. В 1942 г. началась бомбардировка немецких городов, что привело к разрушительным пожарам, которые усугублялись тем, что в строительстве (особенно при устройстве пола), начиная с древних времен и по 1935 гг., широко применялось дерево [Berg, 2006]. Некоторые кровли все еще производятся из дерева, например в Скандинавии. Стены и дымоходы обычно были из кирпича, и сохранились после пожаров [Friedrich, 2002]. В условиях военных действий было принято решение, что новые строительные материалы должны быть огнестойкими и, в связи с лимитированными ресурсами, упор должен был быть на простые сырьевые компоненты. Этот современный аспект весьма важен и в современное время, когда с учетом климатических особенностей мы должны отдавать предпочтение эффективным строительным материалам, которые оцениваются с точки зрения финансовых ресурсов и энергоэффективности. Автоклавный газобетон имеет низкую энергоемкость производства по сравнению с другими материалами. Джозеф Хебель, широко известный баварский строитель, с 1926 г., узнал о новом материале под названием автоклавный газобетон от Главного советника по вопросам строительства, Германа Гислера, который, по приказу правительства, организовал встречу с крупными застройщиками в Южной Германии [L. Hebel, 2008]. Где-то в 1941-42 гг. Д. Хебеля пригласили посетить новые заводы по производству автоклавного газобетона «Siporex» в странах Балтики (Таллинне и Риге) с целью ознакомления с производством армированных панелей. [Rosenborg, 1998]. Это весьма удивительная информация, не с той точки зрения, что инженер занимался профессиональным шпионажем, хотя и с согласия шведской стороны [Jönsson, 2009], а больше с той точки зрения, что это происходило в военное время, когда немецкая индустрия, по приказу Фюрера, полностью была занята производством для военных нужд. По сути, это было преступлением заниматься чем-то, что не обеспечивало военные задачи. Очевидно, внутренние и международные обязательства отличались! Некоторое допустимое отклонение от военного курса может характеризоваться экономической необходимостью в министерстве экономики, где люди, такие как Отто Оледорф открыто планировали дальнейшие перспективы развития Германии, несмотря на запреты. [Herbst, 1982]. Точно неизвестно была ли связь между Олендорфом и Гислером, но это знак того, что даже в Третьем Рейхе были люди разумные, которые готовили условия для будущего развития. Или были ли они настолько убеждены, что войну выиграют, так или иначе? И только после 9 сентября 1943 г., опасная ситуация была изменена по приказу Фюрера, согласно которого началось аварийное жилищное строительство для многих обездоленных людей, которые стали жертвами бомбежек. Вероятнее всего, производство автоклавного газобетона Хебелем в Меммингене с марта 1943 г. было частью этой программы. Джозеф Хебель расширил свой бизнес посредством приобретения в Эммеринге позднее, в том же году, заброшенной фабрики по производству силикатного кирпича, на которой были рабочие автоклавы, готовые к производству. Его офис в Меммингене (с 1921 г.) разбомбили в 1945 г., как раз перед окончанием войны. Впоследствии он начал производство армированных панелей, порезанных из формы тонкой проволокой. Порезка проволокой была известной технологией, используемой, например, в производстве сыра, которая в технологии газобетона запатентована компанией «Ytong» (1942) [Byttner, 1968]. Вероятнее всего, Хебель знал об этом применении.
Джозеф Хебель был талантливым инженером, но не являлся изобретателем. Технология, примененная им в своем производстве начиная с 1948 г. в Эммеринге, была мудрым выбором из уже существующих решений. Рецептура производства автоклавного газобетона была немецкая, а технология порезки пришла из Швеции. Изначально, деньги получили из помощи, предоставленной Германии по плану Маршалла. Хебель специализировался на армированных панелях и элементах, т.е. профиль близкий к производству компании «Siporex». В 1961 г. первый дом был возведен Хебелем и уже в следующем году новое подразделение, «Hebel House», было создано для строительства жилых домов по всей Германии. С тех пор Хебель выкупил несколько заводов «Siporex». В 1980-х гг. [Wittmann, 1992 / Pytlik & Saxena], количество производственных предприятий было приблизительно одинаковым между двумя компаниями и приравнивалось к 35 у каждого. В 1994 г. стало 45 заводов компании «Hebel». В 2002 г. [Charleston RBJ, 2002] количество заводов компании достигло 115, в среднем в год открывалось не менее 4 новых завода. В конце-концов, Хебеля перестали отождествлять с компанией «Siporex». Мировой успех автоклавного газобетона бренда компании «Hebel» является доказательством его высокотехнологических решений в комбинации с практикой превосходного менеджмента. В 2004 г. общее количество заводов автоклавного газобетона по всему миру превосходило 300 [Budwell, 2004], при этом 40% из них принадлежали компании «Hebel». Имя Хебель стало само по себе брендом.
ДАЛЬНЕЙШИЕ ШАГИ РАЗВИТИЯ
Автоклавный газобетон в сочетании с армированием сталью формирует систему строительства, которая должна использоваться исключительно в сочетании со сталью, цементом и иногда деревом. Составы автоклавного газобетона совершенствуются и могут включать в себя компоненты отходов производства (уже в 1950-е годы, на основе патентов 1930-х гг.!), таких как пылевидная зола-уноса, класс F, как частичная замена песка либо являясь единственным кремнеземистым компонентом смеси, при этом исключая энергоемкий процесса помола песка. Это шаг к развитию экологически чистого производства, который направлен на работу в диапазоне низких плотностей материала. В настоящее время его пытаются использовать в системе производства армированных изделий. Согласно опыта «Siporex», во избежание появления продольных трещин было невозможно заменить более чем 70% песка. Однако это заключение ставится под сомнение другими производителями, такими как «H+H Celcon». Способ избежать трещин – это включение в состав рецепта оксида кальцинированного магния. По нашей информации «Hebel» больше не использует золу-унос, после серьезных проблем на тестовом предприятии в 1986 г. Производство стеновых панелей, до 30 м2 возможно при натяжении в одном направлении, вертикальном. Данная технология была разработана на основе технологии монолитных стен Г. Дала [Rosenborg, 1998]. «BCE» система представляет собой технологию полутяжелого строительства. Она несет нагрузку в два раза превышающую собственный вес, в то время как тяжелый бетон несет нагрузку только в половину собственного веса. Считается, что технология «BCE» помогает исправить недочеты традиционной технологии производства автоклавного газобетона, которая очень неэкономно использует сталь, точно так же как технология тяжелого бетона неэкономно расходует цемент. Такой материал нельзя расценивать как дешевый товар в современном мире из-за огромных энергозатрат, связанных с производством цемента, и жестких ограничений на использование природного гравия. Подобные ограничения вероятнее всего будут распространяться и на дробленый камень, который, на данный момент, заменяет природный гравий на рынках скандинавских стран. И зачем разрушать природу без особой на то необходимости? В дальнейшей перспективе развития, мы считаем, цементная индустрия сборных конструкций также будет пользоваться методами «BCE» технологии. В любом случае, новая технология более эффективна, чем изначально используемая.
Bo G. Hellers, Bo R. Schmidt, Autoclaved Aerated Concrete (AAC)-the story of a low-weight material, - Materials of 5th International Conference on Autoclaved Aerated Concrete “Securing sustainable future”, Bydgoszcz, Poland, 2011, - p. 63-68.